Utility safety can sometimes feel like 12-dimensional chess. With hazards coming from all angles — not to mention variables like weather, traffic, and even time of day affecting them — it’s easy for safety professionals to get overwhelmed.
Unless you have a systematic way to identify hazards and make sure you have controls for them in place, your workers face injuries — maybe serious ones.
Every day on the job, safety professionals need critical information:
- What hazards are workers going to encounter today?
- What makes some job activities riskier than others?
- What takes an injury from trivial to life-altering?
- What can you do to keep your workers safe right now?
That’s exactly what safety and risk experts James Upton and Sonam Kala cover in Urbint’s webinar, Setting the Energy Wheel in Motion: How Leading Safety Science and Predictive Insights Help Utilities Prevent Serious Injuries and Fatalities to Their Workforce.
Here’s a rundown of key takeaways from the session, including tips on how to put the latest safety science into action. Read on to learn more (or watch the full webinar here.)
1. Hazard recognition is the first step in staying safe
Most of the current knowledge about safety identification comes from studies on situational awareness: “The process of perceiving an important stimulus, understanding its meaning, and anticipating outcomes,”1 says Upton, director of safety operations at Urbint and former vice-chair of serious injury and fatality research at the Construction Safety Research Alliance.

Situational awareness comes down to four key steps:
- Hazard recognition — Workers notice the presence of a hazard;
- Risk perception — Workers judge how much risk the hazard presents;
- Risk tolerance — Workers decide how much risk exposure to tolerate; and
- Behavior — Workers choose how to behave in response to their hazard assessment.
“Most safety programs focus heavily on this behavior aspect, ignoring the first step in situational awareness: hazard recognition,” says Upton.
That’s a problem. Workers can’t respond to a hazard they don’t notice.
2. The Energy Wheel helps workers recognize >30% more hazards
Fortunately, research over the past decade has made important discoveries about the causes of injuries and how workers’ brains perceive the world.
“Injuries, especially critical injuries, arise from the release of energy,” says Upton, “and there are all kinds of different types of energy on our job site.”
But because of how the human brain has developed, some types of energy are much more easy to spot than others. Workers typically identify about 67% of hazards that involve gravity, but only 40% of electrical hazards, and only 19% of chemical hazards.2
The Energy Wheel is a tool developed to call attention to all energies that show up on a job site, especially the ones that are easy to miss. Workers, supervisors, and inspectors can use it to assess the job site, step by step, to see if any hazardous energy is present that may harm anyone.
3. Higher energy leads to more severe injuries
Hazard recognition is only the first step in staying safe. Not all energy sources you identify are likely to cause a problem. Rather, only situations with large amounts of energy are likely to cause a life-altering or life-ending injury.
“This can actually be quantified,” says Upton.
Hazards with…
- < 350 foot-pounds — Result in first aid;
- 350 to 500 foot-pounds — Result in a medical case or OSHA recordable; and
- > 500 foot-pounds — Result in serious injury or fatality (SIF).
4. 4 simple questions can identify persistent safety risks
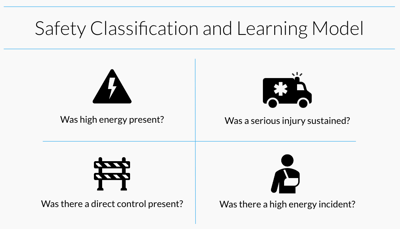
Since this energy theory has become more widespread, construction and utility safety programs have started to focus on the STKY — “the Stuff That Kills You,” says Upton.
The Edison Electric Institute drew on this research to develop its Safety Classification and Learning (SCL) model. This model is designed “to help organizations consistently and reliably classify and define incidents and observations.” Organizations use the SCL model to dial in their safety initiatives on high-energy hazards and direct controls.
At its heart, the SCL model comes down to four questions:
- Was high energy present?
- Was a direct control present?
- Was there a high-energy incident?
- Was a serious injury sustained?
By answering these questions, organizations can better identify scenarios in which their workers habitually face potential SIFs (and then make sure to mitigate those risks in the future).
To help supervisors and inspectors answer these questions, the model includes a set of 13 high-energy hazard icons that represent about 75% of the high-risk scenarios utility workers encounter.
5. Safety is the presence of controls
While knowing about hazardous energy and the 13 high-energy hazards is helpful, this information alone doesn’t keep anyone safe. “Safety is the presence of controls. At its core, fundamental value, that is what safety is,” says Upton.
To make sure all the potential sources of serious injury are controlled on a job site, safety professionals need to perform a high-energy controls assessment (HECA, also known as energy-based observations), concentrating on energy over 1,500 joules.
During these observations, supervisors or safety inspectors move through the job site, looking for scenarios that correspond to the high-energy hazard icons (e.g, suspended loads, falls from elevation, excavations, etc.) Whenever they find a matching work type, they check to see if a direct control is in place.
For example…
- Suspended loads — Are there barricades and exclusion zones set up?
- Fall from elevation — Is fall protection in place and anchored properly?
- Excavations — Has a trench protection system been installed?
If the answer is yes, capacity to fail safely has been created, and the work is ready to perform. (Congratulations to the crew on a job well done!)
If no, there’s an opportunity to stop work, reassess the situation, and put the proper controls in place before proceeding.
6. The challenge isn’t understanding safety — it's a lack of resources to apply that knowledge
The principles of energy-based safety are simple, but putting them into practice on the job can prove much more difficult.

Resources are a common constraint. Contracting crews may know to check for hazardous energy and controls, but staffing shortages, inexperienced workers, and tight deadlines sometimes let best practices fall through the cracks.
“It takes a lot of time and a lot of effort, and rightly so, to do a pre-job assessment for a task where the most likely outcome of a mistake is a serious injury or death,” says Upton.
Likewise, utility safety inspectors often have several job sites to visit each day. They simply cannot do a thorough evaluation for every hazard that might result in a bump or scrape. They need to focus on the STKY.
To make sure the highest-risk tasks get the most safety oversight, utilities and work crews need a way to sort serious hazards from trivial ones. With all the variables and resource constraints involved, though, it’s a challenge to figure out which tasks need that attention — especially across multiple job sites.
This is where Urbint Lens for Worker Safety can make all the difference.
7. 3 precursors to SIFs (and 3 ways to improve job site safety today)
Regardless of resources and budget, there are ways utilities and construction crews can improve their job site safety today.
“Over the last two years, Urbint has been fortunate enough to be involved in some research through the University of Colorado and the Construction Safety Research Alliance,” says Upton. “We wanted to know — ‘What are the things that are always there before the bad thing happens?’
“What we’re able to talk about are the three unique precursors to SIFs.”
Precursor 1: Lack of hazard recognition
Way to Improve: Apply the Energy Wheel to increase hazard recognition
Using the Energy Wheel to walk through all the types of hazardous energy on the job site can increase hazard recognition by >30%.
Precursor 2: Lack of direct control
Way to Improve: Perform high-energy controls assessments (HECA) to ensure controls are in place
High-energy controls assessments make sure you have direct controls implemented for the highest-risk job tasks happening today.
Precursor 3: Lack of pre-job work planning
Way to Improve: Conduct pre-job safety briefings to develop work plans
Taking time to plan your work for high-risk scenarios is key to reducing SIFs.
***
Hazards are unavoidable in utility work. Every day, workers dig trenches, string electrical wires, and trim trees along motorways. But as they perform these vital tasks, they don’t have to put themselves at risk of a SIF.
Take the time to plan out the day’s work. Search for sources of hazardous energy. Ensure direct controls are in place for high-energy hazards. By following these three steps, supervisors and inspectors can keep workers building and maintaining the critical infrastructure the world needs — while moving the risk of SIF closer to zero.
Interested in hearing more about ways to put energy-based hazard recognition into action? Watch our recording of Setting the Energy Wheel in Motion or request a demo of Urbint Lens for Worker Safety to see for yourself.
—1. Endsley, M.R., 1995
2. Hallowell, M., 2020