7 Best Practices for Underground Damage Prevention
Get the whitepaper PDF
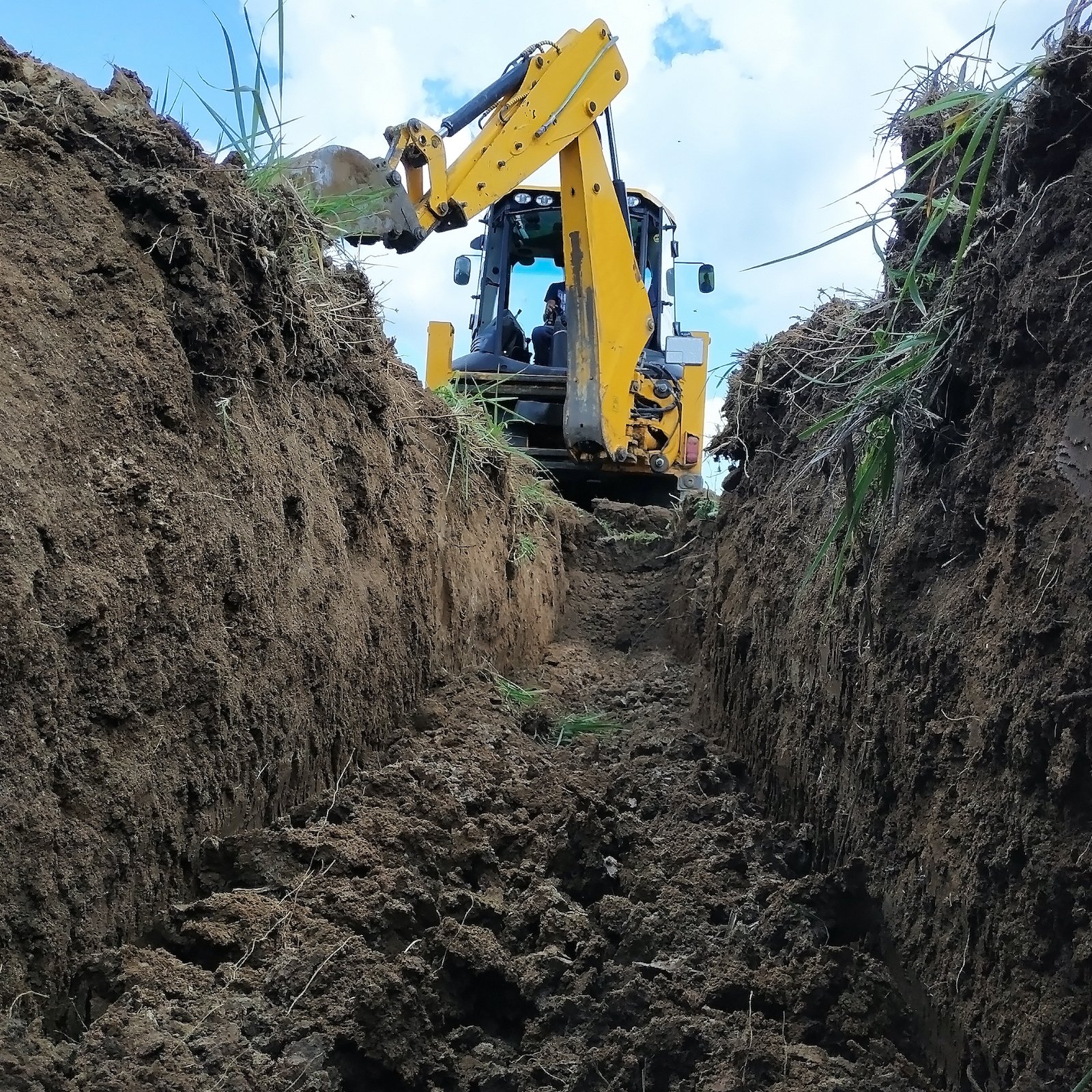
About the whitepaper
Preventing excavation accidents that damage underground utilities is critical to delivering safe and reliable service to customers. In this whitepaper, we discuss seven best practices that damage prevention managers in gas, electric, and telecommunications have implemented to reduce excavation accidents that damage their facilities. Read on for ideas to improve your utility damage prevention program, or fill out the form for your PDF copy.
7 Best Practices for Underground Damage Prevention
Most people don’t think about the important role underground utilities play in their day-to-day lives…until a facility is damaged. Damages to underground gas, electric, telecommunications, and water and sewer facilities are inconvenient at best. At their worst, they threaten people’s lives, property, and livelihoods.
Preventing excavation accidents that damage underground utilities is critical to delivering safe and reliable service. In this whitepaper, we share seven best practices damage prevention teams at utility companies can follow to prevent excavation damages and their consequences.
1. Provide consistent, current mapping to one call centers
Preventing damage to underground utilities is not possible without consistent, current mapping data. One call centers use facility records to notify utility companies when excavators submit their project plans, and locators use them to mark facilities prior to excavation work. Inaccurate or outdated mapping data can lead to utility damages.
Per the Common Ground Alliance Best Practice 6.16 Information Capture, utility companies must collect and provide consistent mapping data for:
- New construction, entered at the time of installation
- The location of abandoned or sold facilities
- Engineering stationing and milepost/marker post location—with latitude and longitude—using common mapping coordinate systems that allow conversion to latitude and longitude
- Alignment of the utility with engineering stationing at each running line change or point of inflection including signs and markers
- Bridges, culverts, and rivers
- All road crossings, overhead viaducts, underpasses—including name of the street—and mile-marker/marker-post designation
- Small-scale maps showing the overall utility route
- Physical characteristics and attributes of the system, such as pedestal, pole, transformer, meter number, anode bed, size, material, product, and pressure
- The number of utility lines or conduits in a corridor or the size of the duct package bank
- Digital imagery used to identify facility locations in relation to the surrounding environment
As you make updates to your facility maps, communicate all additions and changes to the one call center in a timely manner. “It is extremely important [to update] the 811 call centers,” says Kent Kildow, Executive Director of Physical Security at Verizon. “We send a monthly or even weekly update to make sure they've got the latest information on our assets so that we can protect them.”
2. Locate facilities in the time required by state law
Excavators are only required to wait a few days between notifying 811 of their intent to dig and beginning their work. That doesn’t give utility companies much time to dispatch locators to mark their underground facilities, especially during peak seasons.
However, Robert Terjesen, Damage Prevention Manager of Gas Operations in New York City and Long Island for National Grid U.S., says failing to locate facilities on time causes excavators to delay their project starts or to dig without knowing what’s below, neither of which is a good option. Frequently late locates may also lead to more no-call excavations.
“Damage prevention is a shared responsibility. Many of us take that seriously, with the possible exception of this one category: I don't know if we all do the best we can to locate our facilities in a timely fashion,” Terjesen says. “There's trust in the 811 process. And if the owner/operators don't fulfill our end and mark these tickets on time….we begin to erode that trust.”
According to a survey conducted by the Common Ground Alliance, many damage professionals feel managing ticket volume against staffing is “the most significant challenge facing the industry.” Terjeson’s advice for utilities to ensure they have enough staff to accurately and efficiently locate and mark underground facilities is two-fold: Do your best to predict ticket volume, and have staff on hand who can perform locates when volume exceeds expectations.
“You can plan to assume that in a particular month, you need X number of locators. But, projects come from out of nowhere and suddenly you're receiving many more tickets than you anticipated,” he says. “Having a bench on the locate side that, throughout the year, you can use to perform QA audits and things like that, but on very busy days and weeks, you can pull them in and have them locate is critical.”
3. Communicate openly with excavators
It’s in the best interest of utility companies, project owners, one call centers, locators, and excavators to prevent damages to underground utilities. But, successful utility damage prevention requires more than a shared goal; it also requires communication between all parties.
“You need to view the utility, the excavator, the locator, the 801 one call center all as partners,” says Matthew Roesner, Director of Network Services for AT&T Field Operations at AT&T.
One essential form of communication between damage prevention partners is positive response. Utility companies should provide a positive response to all facility locate requests, even if it’s not required by law. A positive response tells excavators that no conflict situation exists or that facility owners or operators have marked the requested area, allowing them to begin work.
Furthermore, excavators should have the ability to get in touch with utility damage prevention representatives by phone or email. This could entail distributing the direct contact information for individual damage prevention team members, or like Baltimore Gas and Electric Company did, establishing a departmental hotline.
“This is a number where [excavators] can speak to one of our inspectors. They’re not just calling the general hotline, talking to a customer service rep, and then going down the line,” says Ian Jones, Damage Prevention Supervisor, Baltimore Gas & Electric. “Us sharing that with anybody and everybody who’s digging shows we’re willing to take their call. More times than not, we can have somebody there [to help them] within 30 minutes.”
4. Use technology to prioritize sites for intervention
Countless excavations happen each day, but only a fraction pose a threat to underground utilities. Manually reviewing all 811 or one call tickets to pinpoint the riskiest excavations is time-consuming, inefficient, and often ineffective, which is why many leading utilities are now using predictive technologies like Urbint Lens for Damage Prevention.
Urbint Lens for Damage Prevention reviews all of a utility’s 811 or One Call tickets and predicts where excavation accidents are most likely to occur or where the consequences of utility damages would be the most severe. With this information, damage prevention managers and their teams can schedule meetings with locators prior to marking or work with excavators to be present at the job site during excavation to protect facilities.
“The higher the risk, the greater the potential for damage on that particular site,” Terjesen explains. “This allows us to be more targeted with our limited resources. Urbint helps us know where to send our field personnel every morning.”
The software takes the guesswork out of field risk management and enables utilities to build risk-driven damage prevention programs. “Urbint is helping us get ahead of future damages. Predictive analytics is the best way in which a facility owner can improve their damage prevention program,” Terjesen says.
5. Engage internal and external teams
Even at large utility companies, damage prevention teams are usually quite small. It’s not uncommon for a single damage prevention representative to cover considerable geographic territory, sometimes the size of an entire state.
As previously mentioned, damage prevention solutions like Urbint Lens for Damage Prevention help managers and their teams prioritize high-risk excavation sites. When it comes to monitoring other sites with less risk, damage prevention experts recommend empowering other company employees to take action.
At Black Hills Energy, Damage Prevention Manager Nathan Stewart implemented a program that allows any employee—meter readers, office workers, even the CEO—to easily report unsafe digging. “Protecting our facilities is the most important thing we can do. If we're all bought in—all 3,500 employees at Black Hills—we can actually make the difference and lower damages,” Stewart says. “It gets more eyeballs on job sites than my team can complete.”
In times when there aren’t enough damage prevention staff to visit high-risk sites, Brad Roulo, Director of Utility Operations for Urbint, advises reaching out to locators for help. “Locators can conduct remote contact with excavators. They can make that initial contact with the excavator to tell them, ‘Hey, we have a critical asset here,’” he says.
6. Be strategic about 811 education
According to the Common Ground Alliance, no-call excavations have made up at least one-quarter of the total reported damages in the U.S. and Canada every year since 2009, except one. In 2020, failure to call 811 was the largest individual root cause of damage, accounting for nearly 32 percent of total reported damages, according to the CGA’s 2020 DIRT Report.
Reasons excavators do not contact 811 about their projects vary. In many cases, excavators simply don’t know the law: A 2020 CGA research report showed half of people said they were aware of the 811 “call before you dig” number. In other cases, excavators don’t think small projects require a call, or they think contacting 811 will delay their project.
To raise awareness of 811, promote compliance, and protect underground facilities, utility companies should launch public education programs. Section 8 of the CGA’s best practices guide focuses on public education and awareness and offers tips utility companies can follow to improve safe digging in the long term.
Importantly, companies must carefully research their target audiences to understand where to reach them and the types of messages that will resonate. “Over the last 20 or 30 years…there have been a lot of mass advertising campaigns and overall TV campaigns, radio campaigns to get general awareness,” Roulo says. “We have to think about how to get more targeted with our advertising.”
“The next generation of excavators are coming down the pike, [and they] are not using the same technologies that we are,” says Kelley Heinz, Senior Claims Case Manager and Damage Prevention Manager at ComEdison. “We've got to look at the target audience that we want to communicate to and understand where they're getting their information from.”
7. Learn from past utility damages
A damage prevention team can do everything in their power to prevent utility damages, but excavation accidents can still happen. When a situation like this occurs, use it as an opportunity to improve future critical infrastructure protection efforts.
Hold a fact-finding review to determine what, if anything, could have been done differently to prevent the damage. For example, you might find a member of the damage prevention team had not been able to make contact with the excavator prior to the project start date, and the excavator was unaware they were digging near critical facilities. Apply what you learn during these reviews to improve your damage prevention process.
Using these best practices, utility companies can prevent excavation damages that threaten the safety of their workers and communities and the reliability of their service. For more damage prevention help, or to request a demonstration of Urbint Lens for Damage Prevention, visit urbint.com.